Let’s talk site logistics! From the initial site setup to bulk and detailed excavation sequencing, to the positioning of temporary resources and workers on the construction site, accurate logistics planning is critical in ensuring the an efficient and productive project. Without proper planning in pre-construction, the cost of manpower, materials and equipment delays affect overall project timelines. As Brent Olund, Vice-President of Sustainable Construction says, “for every extra hour spent in pre-planning it saves more than 4 hours on site during construction.” In this blog, we will discuss site logistics and the keys to effectively planning this process.
Importance of Site Logistics on Construction Sites
With detailed project programs, site logistics planning allows general contractors and construction managers to build a site specific plan that will ensure their team on site will work safely, efficient and maximize productivity which leads to higher margins. Effective planning of site logistics ensures that all human resources on site have a path and know how to exit the site safely at all times, temporary resources are positioned at the optimal locations, material arrives and flows through the site efficiently, traffic management is taken into consideration, staging areas are used to provide access to the build and in general, unforeseen costs and avoidable waste are kept to a minimum. Smooth execution of these aspects enable an agile and productive job sites.
Without good logistical planning, project sites will be disorganized, exposing workers and the public to safety hazards and work will take longer to complete, effecting the schedule. Whether it is the need to maximize tight site space, install cranes or create storage spaces, it is important to build extensive plans for all parts of the construction site logistics operations, in this regard 4D simulations are a great way to plan, communicate and reduce risks on the job.
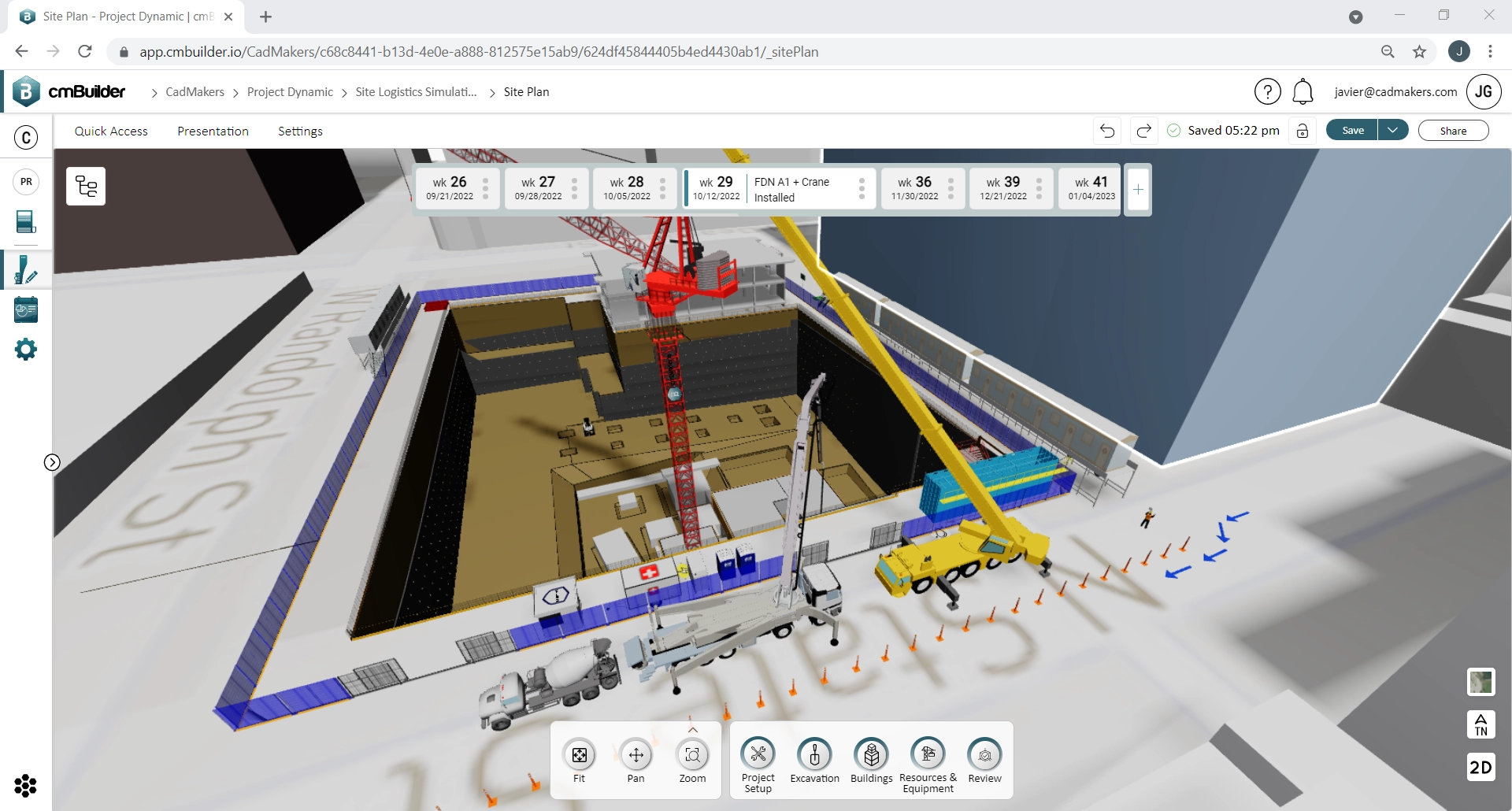
Keys to Logistics planning
Knowledge about the local environment
What is the landscape of the proposed project? Is this an urban space with tight spaces and taller buildings? How are the buildings bordered by street walks and pavements? What time of the year/weather period will each phase of the timeline begin and be completed? Will there need to be trees or other landmarks marked and protected during the build? A pre-construction team should consider where the construction consolidation center or muster point(s) will be located. Local weather forecast should dictate the location of break areas for workers. In places prone to harsh climates, winter requires heated break areas and air-conditioned shades in the summer may do the trick. Always consider dust control measures to curb air and water pollution of the construction site and its surrounding areas. Truck tires may need to be cleaned after leaving the site as to not impact the surrounding area.
Consider the physical elements in and around the site
One of the unique benefits of logistics planning is the insight it provides about the specific site. It is important to ensure that all existing land elements on the site are identified ahead of time.
Access and haul roads, permanent walkways, traffic patterns may need be modified prior to starting construction. Parking for site workers, staging for concrete trucks and temporary signage should also be accounted for prior to scaling up construction on site.
Planning traffic flow
Effective logistical planning requires planning around human, equipment and material movement in and around the site. The size of equipment, volume of vehicles and number of people that will be on site. If your project is around a tight urban space, ensure that site entrances and exits are accessible and construction traffic are on hand to direct traffic. Local jurisdictions may also determine the limitations on potential traffic and should be accounted for. Some cities permit certain types of crane due to airspace restrictions and certain vehicle weight or height limits due to urban town road restrictions.
Planning locations for major temporary resources
It is essential to plan the location of key resources like tower cranes and material hoists. In tight urban spaces this is even more important as the air rights above adjacent properties can determine the type of crane selected and the location. The location of the crane is linked to the location of the material hoist and the loading zones, to ensure efficient crane swing and picks throughout the project. Effective planning and simulation of these key resources can be major drivers of onsite productivity and cost efficiency. This can be the difference between a project being completed late and over budget or early and under budget.
Safety protocols around site and pedestrian proximity
Most importantly, it is critical to plan for the safety of everyone on or around the construction site. From establishing emergency muster points for crews to clearing pathways for emergency vehicles, site logistics must account for every unforeseen scenario. Public safety precautions must be taken in line with local jurisdictions to ensure that construction tools, materials and equipment are used safely on site. With the threat of COVID-19 and its variants, teams must ensure that all local health and safety protocols are met. Break areas, hand washing stations, and all safety protocols must meet the guidelines provided by health authorities.
Want to try cmBuilder out for yourself? You can directly start a free trial on cmBuilder.io today! You can also schedule some time and book a customized demo with a product expert!